Due to the "wet and hot curing" process of the flow line process is carried out in the maintenance pit with thousands of scattered parts. Pit loading and unloading operations are tedious and labor - intensive. Therefore, in the later production of twin block concrete sleeper, we also tried the transfer process with continuous transmission as the main characteristic of "curing kiln". Including plane transfer process and three - dimensional transfer process two.
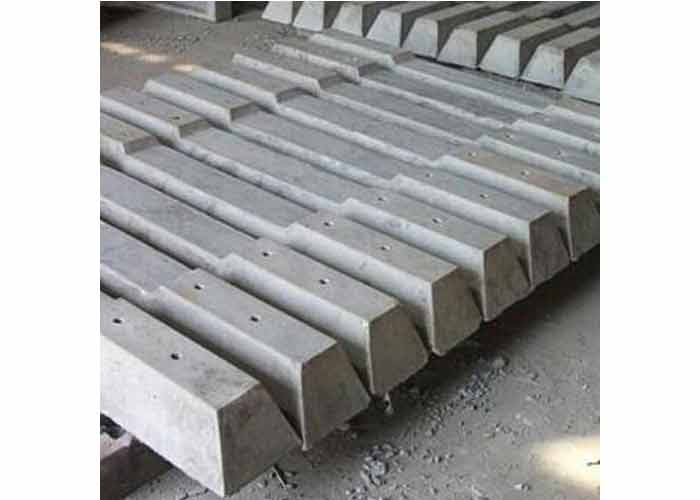
Compared with the intermittent curing pit adopted by the continuous curing kiln and the flow line, the intermittent curing pit has less investment and stronger adaptability, but it consumes a lot of heat and is not conducive to the transition to automation. Continuous curing kiln, can realize automatic production, small consumption of steam, but a large investment and consumption of steel.
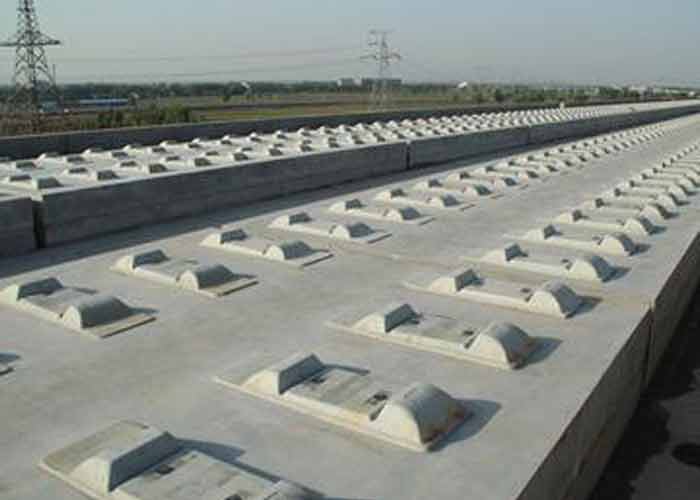
The method is to complete the production of double block concrete sleeper products on the fixed pedestal with a length of 100-150 meters. The production cycle of double block sleeper products is equivalent to the turning period of the pedestal. The main technical equipment and production process are as follows:
1. The seat is 150 meters long and 2.4 meters wide, the wontons are set at both ends along the length direction, and the steel wire tension is transferred to the wontons through the steel beam, making it bear a total tension of 3*30 tons.
2. Each pedestal is divided into three rows for perfusion molding, which can produce 3 x57= 171 double block sleeper at one time.
3. The extension length of the long steel wire is large, so the hoist is used for group tension. Then 60 tons of jack for pre - check.
4. Adopt "low-fluidity concrete" pouring double-block sleeper. The mixed soil is vibrated by an attached vibrator.
5. The turning period of long line pedestal is 5 days, which is calculated as 25 working days per month. It can be turned over 5 times. Therefore, each platform produces 855 double block sleeper every month. Each stand produces 10260 pieces per year. The annual production of 10 pedestals is 102,600.